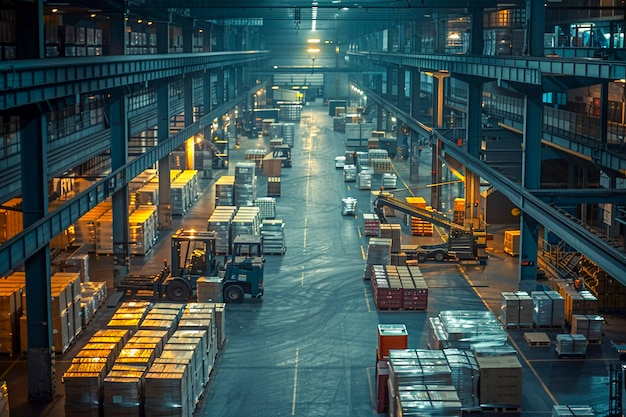
In the fast-paced world of logistics and inventory management, warehouses are the beating hearts of supply chains. Yet, as consumer demands skyrocket and the pressure to deliver intensifies, many warehouses find themselves teetering on the brink of chaos.
Picture this: a bustling warehouse, once a well-oiled machine, now grappling with inefficiencies, misplaced goods, and overwhelmed staff. The stakes are higher than ever, and the consequences of mismanagement can lead to catastrophic meltdowns, both operationally and financially.
Enter automation: a revolutionary force poised to transform these bustling hubs into streamlined powerhouses. From robotic pickers gliding through aisles to sophisticated software that predicts inventory needs, the right automation strategies not only alleviate stress but also empower warehouses to operate with precision and agility.
The question isn’t whether automation is necessary; it’s how swiftly you can embrace it to avert the impending crisis and secure your warehouse’s future.
Understanding Warehouse Meltdown: Key Indicators to Watch
In the fast-paced world of logistics, a warehouse meltdown can strike without warning, manifesting in various telltale signs that demand immediate attention. Perhaps you’ve noticed a sudden uptick in order delays or an increase in picking errors; these are often the first symptoms of an underlying issue.
Inefficient inventory management might lead to stockouts or overstocks, creating frustration among your workforce and customers alike. Additionally, mounting operational costs can indicate that your current processes are stretched thin, struggling under the weight of outdated systems or insufficient staffing.
Pay close attention to employee morale as well; a disengaged workforce often signals deeper systemic problems that could escalate into a full-blown crisis. By monitoring these key indicators, you can proactively implement automation strategies that not only alleviate pressures but also transform your warehouse into a well-oiled machine, poised for success.
Cost Savings: Automation as a Financial Lifeline
In today’s fast-paced economic landscape, the implementation of automation in warehouse operations emerges not merely as a trend but as a strategic imperative for cost savings. Imagine a bustling warehouse floor, where each movement matters, and the slightest inefficiency can translate into significant financial loss.
By integrating automated systems—such as robotic pickers, inventory management software, and AI-driven analytics—businesses can streamline their processes, reducing labor costs and mitigating human error. Consider the stark difference between manually tracking inventory and leveraging real-time data insights; the latter not only accelerates decision-making but also diminishes waste and overstock scenarios.
The initial investment may seem daunting, yet the long-term savings on labor, increased throughput, and optimized resource allocation can dramatically enhance profitability, turning automation into a vital financial lifeline that safeguards against the sporadic surges and bottlenecks characteristic of warehouse operations. Ultimately, embracing these technological advancements is not just a matter of efficiency—its a calculated move that can redefine the financial future of your warehouse.
Future Trends: The Evolution of Automation in Warehousing
As we look to the future, the landscape of warehouse automation is poised for transformative advancements, driven by emerging technologies that promise to redefine operational efficiency. Imagine a facility where drones flit through the aisles, delivering goods alongside autonomous robots that navigate intricate layouts with ease.
The integration of artificial intelligence will not just streamline logistics; it will revolutionize decision-making processes, allowing for predictive analytics that anticipate goods movement before the demand spikes. Moreover, the rise of IoT devices will enable real-time tracking and monitoring of inventory, fostering an agile ecosystem that can respond to fluctuations in consumer behavior.
But it doesn’t stop there—collaborative robots, or cobots, will work side by side with human workers, amplifying productivity while enhancing safety protocols. In this evolving symphony of technology, warehouses will not just adapt—they will thrive, turning the threat of meltdown into a catalyst for innovation and growth.
Conclusion
In conclusion, the implementation of automation in warehouse operations is not merely a trend, but a strategic necessity to avoid potential meltdowns amidst increasing demands and complexities. As businesses strive for greater efficiency, accuracy, and adaptability, technologies such as robotics, AI-driven inventory management, and automated order fulfillment systems can significantly enhance productivity and reduce errors.
TWA Warehousing exemplifies how automation can transform traditional warehousing processes into streamlined, responsive operations that meet modern challenges head-on. By embracing automation, warehouses not only safeguard against operational crises but also position themselves for sustainable growth in an ever-evolving market landscape.